Last updated: 25 May 2022
Driving down the maintenance costs of tidal turbine blades is one of the main objectives of the NEMMO project. Aiming to improve the material performance of tidal blades, a set of tailor-made testing procedures was developed to carry out a sizeable experimental test programme in a cavitation tunnel at SSPA’s facilities in Sweden. These testing procedures for integrated harsh marine stresses enable the replication and modelling of composite blade lifespan, cavitation wear rates, bio-fouling growth, ageing in a harsh marine environment and hydrodynamic performance.
After carrying out Large Eddy Simulations (LES) and experimental modelling for turbine blade operation, NEMMO project team has identified the best performing Active Flow Control (AFC) strategies. It did this using open-source software OpenFOAM to evaluate the original Magallanes blade, integrating the AFC appendages and novel blade design in model scale. These tests were carried out under real operation and cavitation tunnel conditions.
Three sets of blades – carbon fibre blades from Canoe and bronze blades from SSPA – were used to perform the tests at two tailor-made test rigs designed and built by SSPA to analyse the performance and efficiency of the actual turbine blade in model scale.
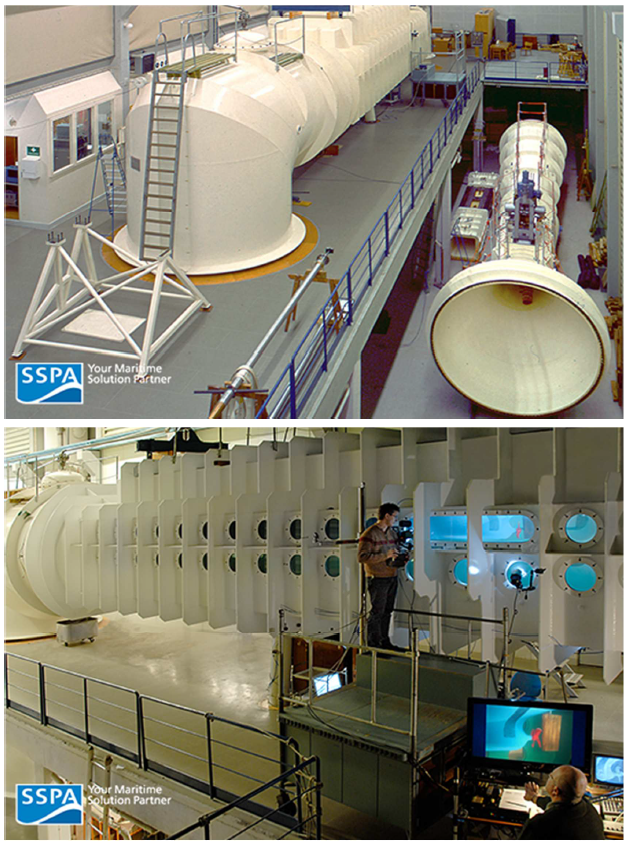
Due to the constraints on the size of the testing section, the novel blade design in model scale was defined and produced with a scale factor of 38.
Flow control experiential tests with constant cross-sectional profiles were carried out on the original Magellanes blades. Instead of rotating, the profiles were attached to the roof of the SSPA cavitation tunnel on a rotating table to be able to test a range of angle attacks. These blades were tested under various tunnel flow speeds and pressure to measure the lift and drag coefficients of the hydrofoil in two sections of the actual blades. The team used this data to verify the Computational Fluid Dynamics (CFD) simulation and investigate the flow control methods’ effectiveness. Read more about this experiential approach.
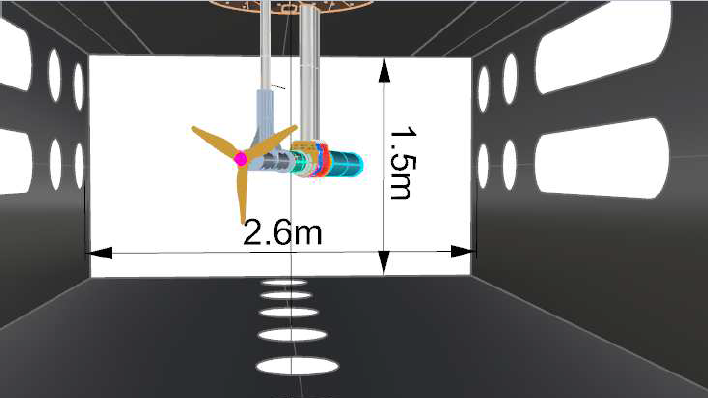
The project team compared carbon fibre blades and bronze blades for blade material testing. Both the SSPA bronze blades and CANOE’s carbon fibre blades were run at 12˚ pitch angle at 0˚ yaw. The difference is relatively high, at points up to 20% in thrust. The carbon fibre blades were made with coating and polished for a smooth surface. For this reason, the blades may not meet the necessary geometrical tolerances compared to the bronze blades. Also, a thickness difference of 0.6mm was measured while balancing the CANOE blades.
The cavitation tunnel testing found that the bronze blades have performed better than the carbon fibre blades, since the blades made from carbon fibre did not have sufficient tolerance for the model test. Therefore, the remaining model tests were completed with only the bronze blazes.
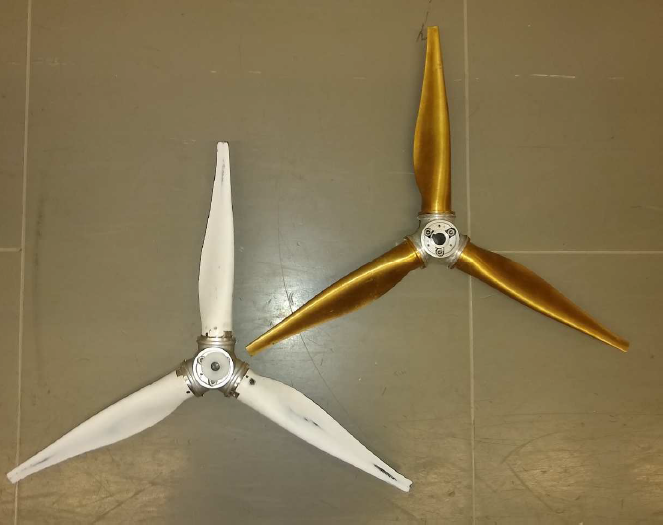
Regarding the performance of the turbine blade, an investigation of the influence of cavitation and translation due to the yaw of the turbine was performed at four different yaw angles between 0 and 19.5 degrees and four pitch angles in different tip speed ratios. Initial measurements were for quite high pitch angles (+12 degrees) and showed no cavitation influence. However, tests at a later stage chronologically at 0 degrees pitch angle showed the influence of cavitation visually and in the measurement data. Again, this is the case at high tip speed ratio, but less so closer to maximum Cp and beyond stall angle.
As the initial results showed no influence of cavitation, the pressure for the first tests was at atmospheric pressure. The remaining tests were completed at overpressure, which was the actual hydrostatic full condition for the turbine.
Turbine’s torque and thrust were measured in SSPA’s cavitation tunnel. Flow velocity measurement in different positions in upstream and downstream of the turbine is needed to improve the turbine’s performance and interaction between two turbines in different yaw angles.
The first blade geometry was tested with Laser Doppler Velocimetry (LDV) to measure the flow field at three planes upstream and downstream of the blades to improve the turbine performance and interaction between two turbines at different yaw angles. LDV measurement is a non-intrusive method to measure velocity components of a position inside the flow by focusing two laser beams through the test section’s window.
Dantec dynamics’ solid-state laser was used to generate two laser beams in different wavelengths to measure two components of the velocity simultaneously. Beams were focused using a lens located under the test section. The laser and lens were mounted on a 3D traverse system to allow the point measurement movement in the volume in the flow field visible through the access window.
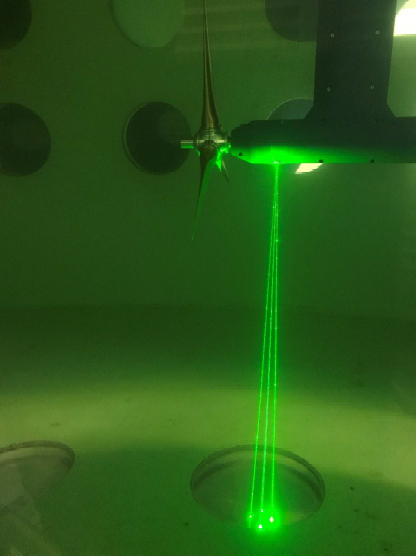
Velocity measurements were performed in 3 planes. Plane 1 was positioned 0.75R upstream of turbine blades; Plane 2 was 0.75 downstream of turbine blades, and Plane 3 at the position of the downstream turbine blades. The image below shows the turbine at a 19.5 degrees yaw angle, with the windows at the bottom of the section (illustrated by circles).
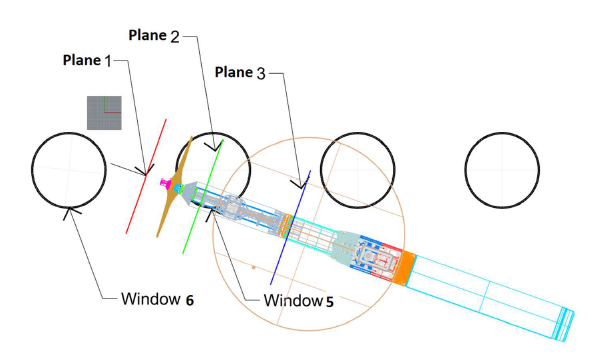
The image on the left shows the results of the velocity magnitude in two planes. The upper section of the planes was not visible through the bottom window and thus was not measured. All measurement data is available in this report.
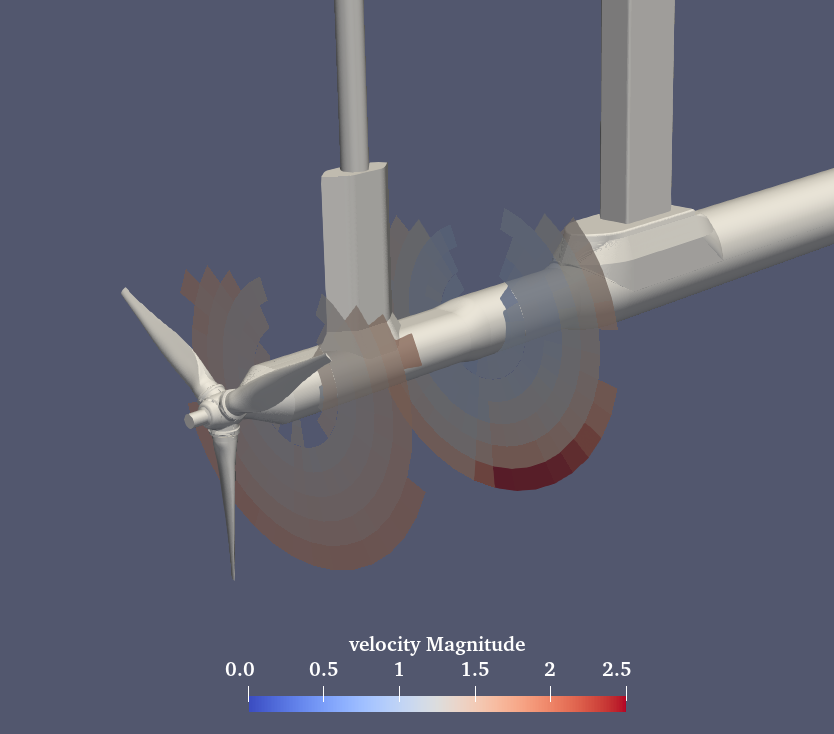
The second blade geometry explored the asymmetrical profile between the leading and trailing edge. As the turbine worked with the flow in both directions, losing some efficiency with a less efficient profile, it could be beneficial when the flow direction is reversed.
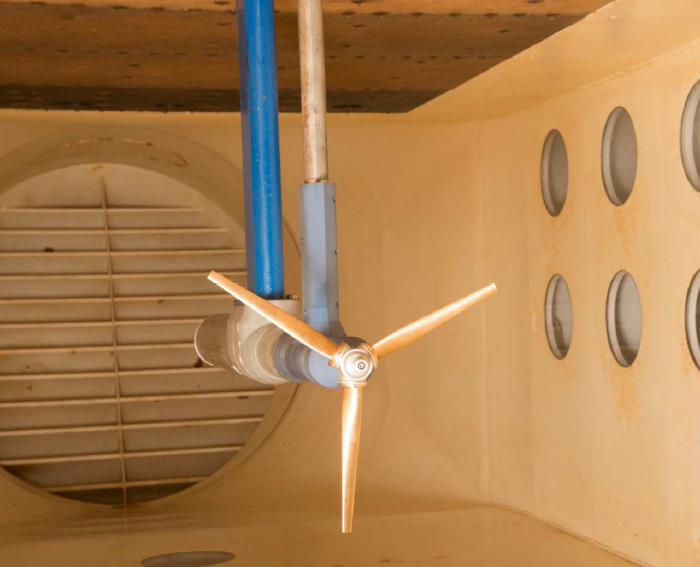
Finally, one of the anti-fouling strategies investigated in Work Package 3 involves the modification of the turbine blade surfaces using bioinspired textures designed to disrupt biofilm growth. The suitability of the Large Eddy Simulation – Actuator Line Method (LES-ALM) methodology for micro-textured blade surfaces has been investigated through a combination of high-fidelity wall resolving turbulent flow simulations of the NEMMO blade surface and textured surfaces.
A detailed turbulent flow simulation study was conducted to assess the impact of the blade surface micro-texturing on the airfoil hydrodynamic characteristics. This study also determined whether the high-fidelity LES-ALM strategy should be adapted to account for surface roughness.
This assessment has relied on a 2-dimensional wall resolved simulation of turbulent flow over one of the single blade sections studied in SSPA’s cavitation tunnel.
The section selected is slice S9 of chord length C = 0.72m. The airfoil was simulated at a tidal stream velocity of 2.5 m/s and a turbine rotational speed of 16.8 rad/s, giving a tip speed ratio of 6.7 and an Angle of Attack (AOA) of 5.46°.
Surface roughness is known to alter the turbulent energy production cycle when the roughness height is greater than a few wall units. As an anti-fouling strategy, the roughness structures proposed in Work Package 3 are based on arrays of elongated rectangular bars or cavities.
Two types of the textures were assessed:
Cavity design: a cavity design is made of rectangular constant depth grooves etched into a flat surface. The groove width as defined in the context of d-roughness refers here to the length of the cavity in the streamwise direction noted Lx. The cavity depth Ly is the roughness height. The width of the ridges between successive cavities is w = 10 μm and is unchanged in the spanwise and streamwise directions. The proposed dimensions are determined by a mixture of factors related to biofouling, structural rigidity and wear. The ridge width must be as close as possible to 10 μm or lower to disrupt the settlement and growth of micro-organisms effectively.
Raised design: the raised rectangular bars are based on the same individual roughness element size and geometry, but the elements are added to the smooth surface rather than being recessed. This creates a fundamentally different flow as the groove width as defined in the k-roughness terminology is the gap width w = 10 μm rather than Lx.
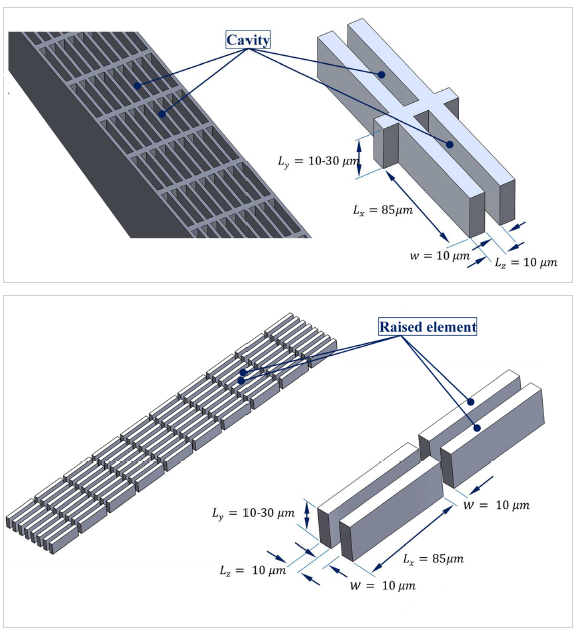
The results showed that both types of textures proposed as an anti-fouling strategy are expected to have a minimal effect on the turbulent flow profiles in the overlap region of the boundary layer over the turbine blade surface. It is possible that an earlier transition to turbulence can result from increased roughness. Based on the results, it is confirmed that no modification to the LES-ALM solver is required.
Based on the available data from the cavitation tunnel and the outcomes from the open-source software OpenFOAM, the different developed solutions will be evaluated in the next task in terms of coefficient of performance, lift and drag ratio, cavitation attenuation and reduced velocity, loads and moments profiles.
The new set of testing procedures for integrated harsh marine stresses was used for applying the AFC strategies further in the verification of CFD simulation and the investigation of the effectiveness of flow control strategies in the next Work Package.
This report describes all the methodologies and results of these tests in detail.